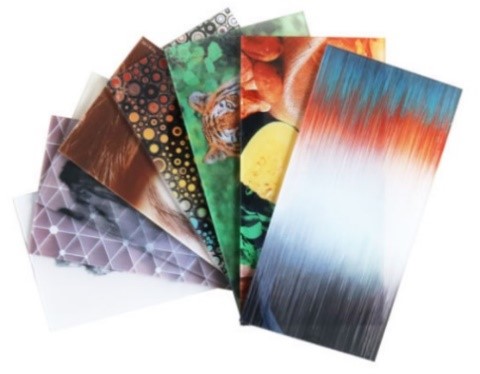
Static electricity creating problems in digital inkjet printing
Digital printing is becoming popular in more and more markets nowadays. However static electricity can create a lot of problems like (printing) errors. Problems that can occur are dust attraction, bad (un-sharp, blurry) printing results or dirty printing heads (so short production runs). Even machine stops can be caused; all resulting in more expenses, so non-competitive printing.
Manufacturers who (single pass) digital-print flat surfaces like paper, cardboard, wooden floorings and especially plastic sheets can experience multiple problems in their printing sections caused by high static charges. To solve this issue, different static measurements are made to learn exactly where the static is generated and where to neutralize, using a FMX field meter or inline static measurement.
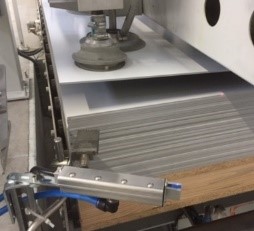
During de-stacking, the single sheet wants to stick to the pile because of static: blowing ionised air between the sheets with (flat-) ionizing air-nozzles or air-knifes with antistatic bar will solve this problem so only a single static neutral sheet will enter the line. During transportation, the sheet is cleaned by ionised air, using the Typhoon system or using a (rotating) brush in combination with an industrial static eliminator. After corona treatment of the plastic sheets again discharging is needed to make sure the treated sheet continues its way without static charge.

Note: Drawings and pictures do not show the application one to one, but clarify the situation and approach reality
When entering the digital printing area with several printing heads, a predefined low static level is needed to guarantee high quality printing and continuous clean printing heads which results in long production runs. To achieve this a Simco IQ Manager System can offer real-time managing and monitoring options with a full controlled Closed Loop Feedback system (CLFB). This system monitors and controls all connected static devices and can be directly connected to the machine PLC via Fieldbus connection. In-line measuring and datalogging of static charge levels can be used in quality reporting.
This provides all information about the efficiency and required maintenance of the bars, as well as the static charge including alarms and other options to increase the control of the line, safety and quality which all results in high quality competitive digital printing!
Interested to learn more about the effect of static electricity?
Find a Simco representative near you.
Please visit www.simco-ion.co.uk or subscribe to the Simco Europe Youtube channel